Health and Safety
Overview
We are committed to keeping our people safe.
Safety is more than a priority for us. It is our way of life. It is a core value that makes us Enbridge.
Our commitment to safety is based on caring for employees, our contractors, the communities where we live and work, and the environment. This commitment is reflected in our new strategic plan released earlier this year: Focus on safety and operational reliability.
We are on Our Path to Zero incidents, in which safety is everyone's responsibility, leadership is accountable for safety performance, continuous improvement is required, hazards are controlled and our commitment to caring extends beyond the workday.
2 performance objectives:
- Strengthening Enbridge’s safety culture
- Ensuring safe workplaces for employees and contractors
2017 Highlights
0 employee and contractor fatalities
Management Approach
In order to continually enhance the safety of our workforce, we have comprehensive strategies, policies, practices, systems and controls in place across the company to protect employees, contractors and sub-contractors. We take a proactive approach to identifying and preventing safety issues, take immediate action when an issue is identified, and continually look for ways to improve our safety performance
In 2018, we are undertaking plans to establish a centralized safety and reliability team serving Liquids Pipelines, Major Projects and Gas Transmission & Midstream. Centralizing our safety teams under one umbrella will ensure that we apply the best in safety standards, policies and practices in a consistent manner across the organization and in the most effective way. The driver of this centralization is to drive even greater safety performance and safety culture across the organisation.
Health & Safety Improvement Strategy
Our vision is to be the leading energy delivery company in North America. This includes being the leader in safety and operational reliability among our peer energy infrastructure companies and driving a strong performance-based safety culture. We are focused on mitigating incidents due to human factors, creating an enterprise risk framework and improving process safety management.
Enbridge Management System Structure
Our primary duty is to keep our workforce safe, protect the public and the environment from harm, and ensure the safe and reliable operation of our assets; and our goal is to maintain and continually improve upon our safety and reliability performance.
This requires us to do the right thing, the right way, every time by conducting our activities in a systematic, comprehensive and proactive manner that manages risks and prevents incidents across the lifecycle of our assets―from design, procurement, construction and operations through to abandonment.
Following our combination with Spectra Energy in early 2017, we established an Enterprise Management System Structure to help us achieve this level of discipline and drive continual improvement in our safety and reliability performance.
This robust structure sets enterprise-wide minimum requirements and guides implementation of these requirements by our business segments. Built into this structure are all dimensions of safety and reliability, including risk management and process safety. The prevention of catastrophic incidents is crucial, and this structure allows us to mandate the application of systematic risk management―good design principles, engineering, and operating practices―throughout the company. As part of this structure, our leaders are responsible for developing and supporting improved safety performance and a positive safety culture, as well as for demonstrating and exercising safety leadership. In addition, all workforce personnel―employees and contractors―have a role to play in helping us sustain our strong safety culture, including the responsibility for reporting hazards, potential hazards and incidents.
Safety Principles and Lifesaving Rules
Our Safety Principles outline how we think about health and safety at Enbridge, and support our core values of Integrity, Safety and Respect by guiding our actions, policies, procedures and culture. The Safety Principles complement our six Lifesaving Rules that focus on areas of high risk and high consequence, which have been updated in 2017 due to the integration with Spectra Energy.
Safety and Reliability Programs
For us, strong safety performance requires a multi-layered management approach to promote and support individual and team contributions. Senior management annually sets detailed safety performance metrics at the business-segment level. These metrics help us focus on key performance factors related to safety and operational reliability. These metrics are incorporated into our business segment scorecards and account for a minimum of 20 percent of the business segment performance bonus available to employees.
We consider our contractors and sub-contractors to be our partners in safety and expect them to view safety the same way we do. In 2016 we did quite a bit of work around our Enterprise Framework for Contractor Safety Management, however due to the combination with Spectra Energy this framework has not yet been implemented. We look forward to continuing this work into 2018 while still having in place our wide range of ongoing contractor safety processes and programs to help us achieve our goal of industry-leading safety performance.
2017 Performance
Strengthening Enbridge’s Safety Culture
For Enbridge, safety culture is our shared attitudes, values, norms, beliefs and practices with respect to safety and risk. Essentially, our safety culture is how we talk about, think about, plan for, act and interact when it comes to safety. It is reflected in our policies, procedures, programs and systems, and in our decisions, actions and interactions, as individuals and as an organization, every moment of every day.
In 2017, we continued to take multiple steps to strengthen our safety culture.
Safety Culture Integration
Immediately following our combination with Spectra Energy in February 2017, we began an across-the-board review of our safety programs and procedures to ensure thorough and effective integration. For example, as part of this process in 2017, we updated our six Lifesaving Rules that all Enbridge employees and contractors are required to follow. Our integration work is continuing in 2018, and we will report on our progress in our 2018 Sustainability Report.
Safety Culture Framework
In 2017, Enbridge moved closer to finalizing the Enbridge Safety Culture Framework (ESCF) and, more importantly, the supporting safety culture assessment toolkit and implementation strategy. We were able to complete a pilot of the Safety Culture Assessment in portions of the business, yielding results that not only supported our assessment protocol, but also indicated a continued healthy safety culture relative to prior assessments.
Looking ahead, we will publish the ESCF internally, and the Safety Culture Assessment and Monitoring Process will progress significantly in 2018 and 2019, resulting in enterprise-wide assessment and monitoring activities. These activities will allow for more frequent pulse checks of the safety culture across the organization. This is important because safety culture drives safety performance. The stronger our safety culture, the better we are able to prevent incidents before they occur, keep our safety systems and programs strong and effective, and ultimately protect ourselves, those around us, our communities and the environment from harm.
The Theopolis Holeman Safety Award is named in honor of a former Spectra Energy leader known and respected for his unwavering commitment to safety. An ardent proponent for operating with integrity and excellence, Theopolis Holeman was instrumental in building and championing our safety culture. Now in its third year, the award seeks to recognize those who share Theopolis' commitment to safety. Nominations are submitted from Gas Transmission & Midstream, and the recipient is selected by GTM leadership.
Bruno Demers, an operations/maintenance supervisor on our T-North Pipeline System in British Columbia, was the 2017 recipient of Enbridge's Theopolis Holeman Safety Award, which is named in honor of a former company leader known and respected for his unwavering commitment to safety.
Bruno has been a champion of personal and process safety throughout his career at Enbridge. He sets high expectations and standards for himself and his team, and above all else has established a strong culture of safety.
“Bruno has also done an excellent job of recognizing the value and strength of our management systems and programs, implementing them and flowing them through how we do our work every day,” said Michele Harradence, Vice President, Gas Transmission and Midstream Operations. “He’s an exceptional safety leader.”
Addressing Human Factors
Since 2014, we have been focusing on human factors, which encompass the way people interact with one another, systems and their environment, and how our human biases and tendencies can lead to unsafe decisions and actions even when we think we are being safe. We are working to maintain awareness and understanding of human factors within Enbridge, and within our industry through several initiatives including online training, development and communication of a series of case study graphics, and sharing foundational safety stories with employees across the organization. We have also shared our materials and learnings with industry and take advantage of our industry association relationships (API, AOPL, AGA, CGA, SGA, INGAA, etc.) to share lessons learned in structured forums established by these associations.
Promoting Driving Safety
At Enbridge, we take driving safety very seriously and provide all of our employees with various levels of driver training and learning opportunities in an effort to ensure that not only our team members, but also their family members and those sharing the road, are safe.
We are standardizing driving safety across Enbridge through our Driving Safety Network (DSN), which is a group of safety and operational specialists who oversee fleet programs and driver-safety programs in each of our business segments. The mandate of the DSN is to align our approach to driving safety and share advancements in technology and training to help ensure the safety of our fleet-vehicle and non-fleet drivers.
In developing a consistent approach to driving safety across the Enbridge enterprise, the DSN will be implementing a Driving Safety Standard and related programs in 2018 and 2019, as well as continuing to advance driving safety improvements.
In 2017, Motor Vehicle Incident rates declined during the combination of Enbridge and Spectra Energy due to the focus on motor vehicle safety that was present in both companies prior to the combination. Looking ahead, this area of safety will continue to be a major focus for us. We cannot and will not allow complacency to set in.
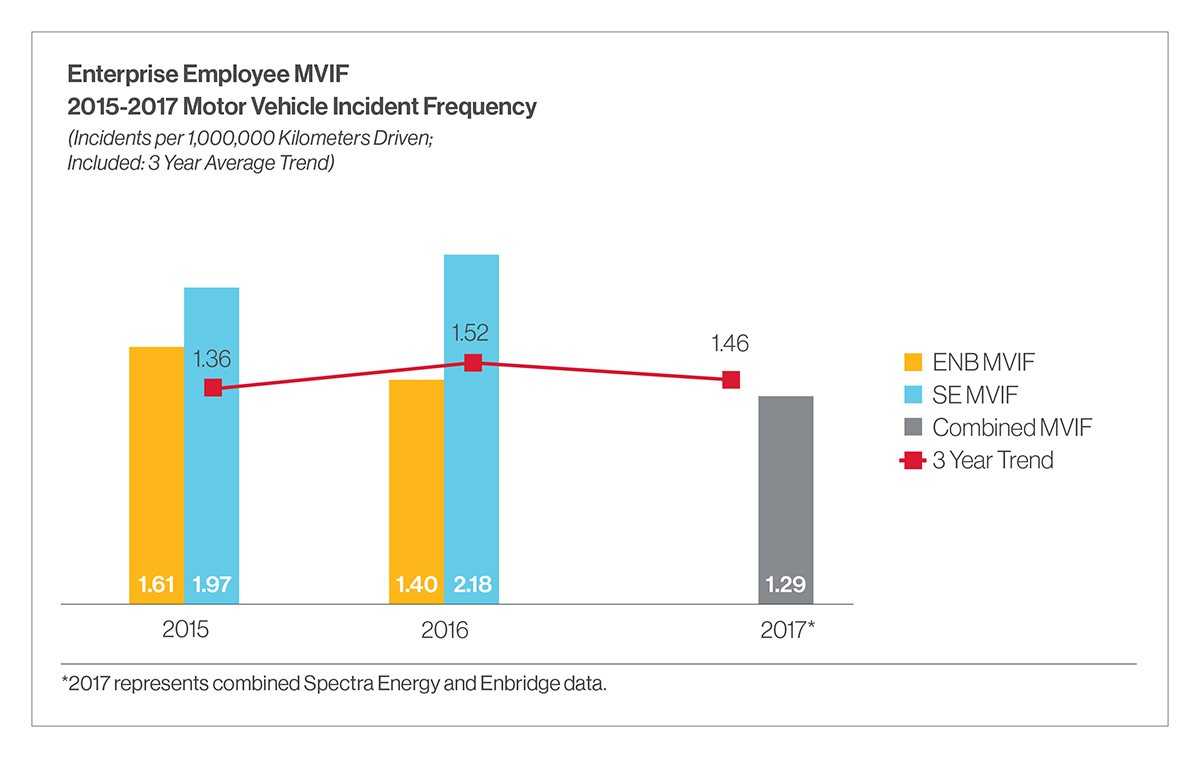
Looking Out for Safety
Our employees and contractors contribute to Enbridge’s safe and reliable operations by keeping safety top of mind in all of their actions and decisions.
They also contribute by performing proactive, formal safety observations on each other. Properly conducted safety observations provide an opportunity to address and measure both desired and at-risk behaviors in a systematic way, thereby driving improvement.
Ensuring Safe Workplaces for Employees and Contractors
Employee Safety – At Enbridge, the safety of our employees is of utmost importance. It is not only a priority for us; it is a core value. To protect the safety of our workers, Enbridge has comprehensive policies, practices, systems and controls in place. We take a proactive approach to identifying and preventing safety issues, take immediate action when a safety issue is identified and continually look for ways to improve our safety performance.
In 2017, during the combination of Enbridge and Spectra Energy, our three-year average trend in Total Recordable Injury Frequency (TRIF) continued to improve and is well below the industry average of 1.0. In total, we had 95 recordable employee injuries, compared with 44 recordable injuries at Legacy Enbridge (ENB) in 2016. This increase is due to the merger with Spectra Energy, which increased the number of employees.
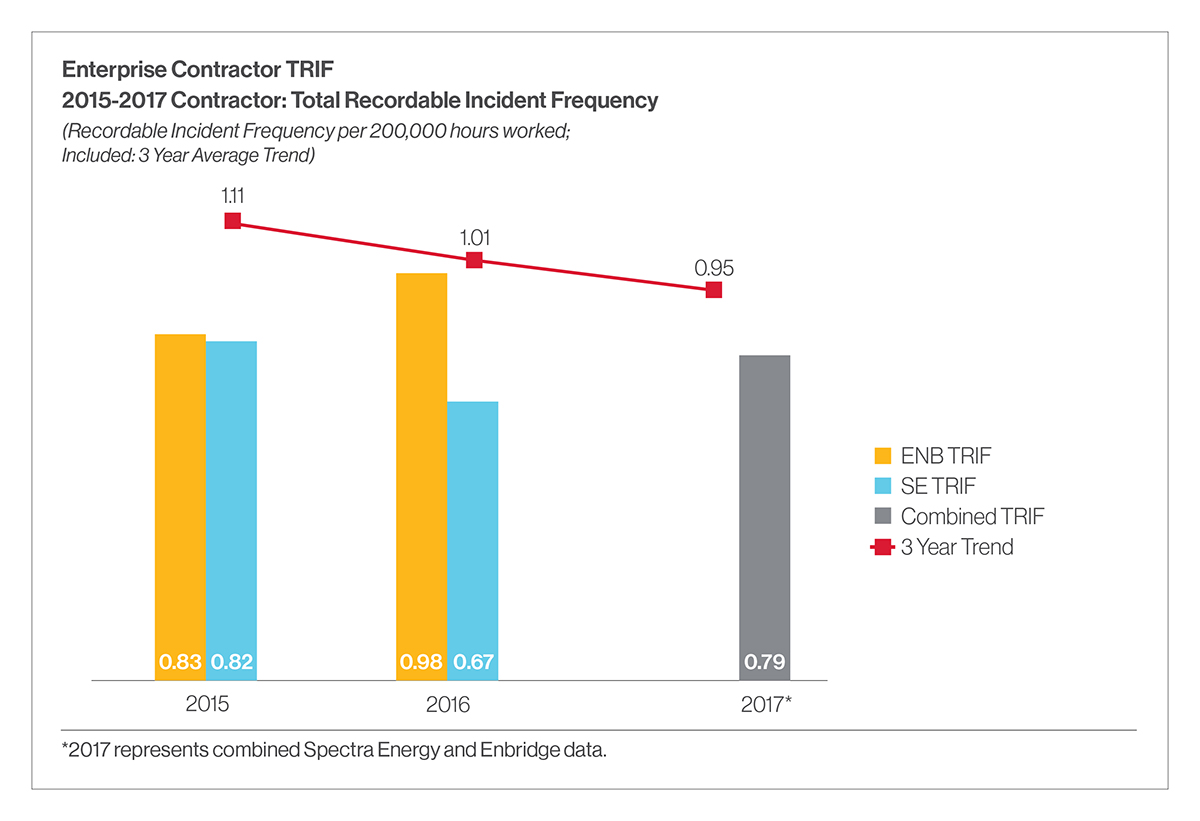
Days away injuries in comparison to previous years saw an increase in 2017; however the rates themselves remain extremely low.
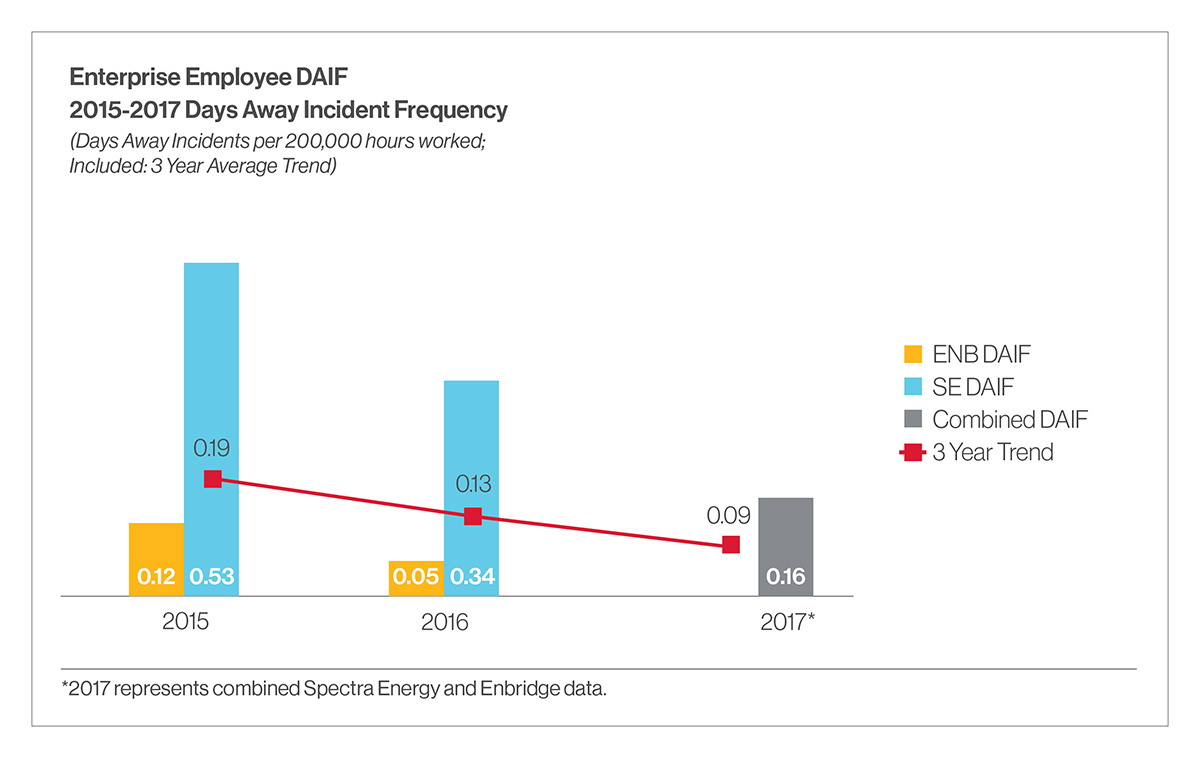

Health and Safety Performance Data Summary 2017 | |||
---|---|---|---|
2015 | 2015 | 2017 | |
Promoting Safe Driving | |||
Motor Vehicle Incident Frequency | |||
Legacy Enbridge | 1.61 | 1.40 | N/A |
Legacy Spectra Energy | 1.97 | 2.18 | N/A |
Enbridge | N/A | N/A | 1.29 |
Ensuring Safe Workplaces for Employees and Contractors | |||
Total Recordable Incident Frequency | |||
Legacy Enbridge | 0.66 | 0.55 | N/A |
Legacy Spectra | 1.03 | 0.78 | N/A |
Enbridge | N/A | N/A | 0.72 |
Enterprise Employee Days Away Incident Frequency | |||
Legacy Enbridge | 0.12 | 0.05 | N/A |
Legacy Spectra | 0.53 | 0.34 | N/A |
Enbridge | N/A | N/A | 0.16 |
Enterprise Contractor Total Recordable Incident Frequency | |||
Legacy Enbridge | 0.83 | 0.98 | N/A |
Legacy Spectra | 0.82 | 0.67 | N/A |
Enbridge | N/A | N/A | 0.79 |
Complete Health & Safety Data is available here.