Maintaining the Fitness of Enbridge's Systems & Detecting Leaks
Overview
2 performance objectives:
- Preventing spills, leaks and releases
- Maintaining the integrity of all our pipelines and facilities
2017 Highlights
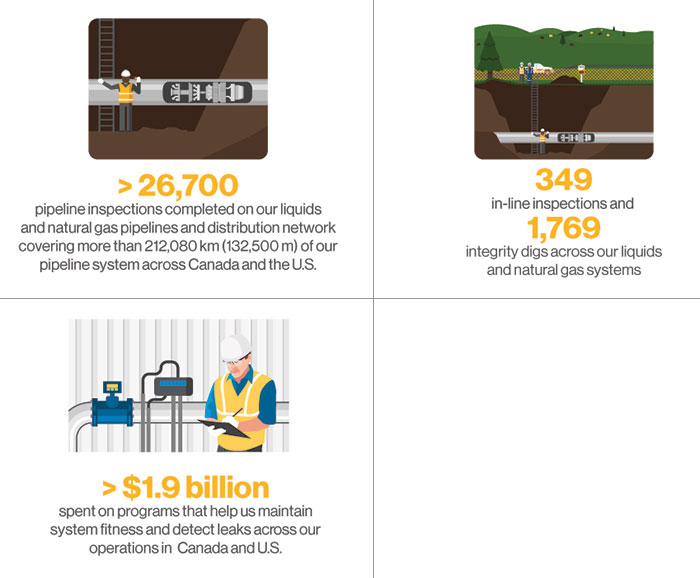
Management Approach
Operating Discipline
Management systems provide an overarching framework for the various actions and programs we carry out to maintain the fitness of our pipelines and facilities. All of our business segments employ management systems that must meet enterprise-wide requirements for mandatory protection programs and standards for rigor and effectiveness, but are tailored to the uniqueness of each business segment’s operations. These systems represent the rules and the checks and balances that help us to prevent human errors and continuously improve the safety and reliability of our operations.
We recognize the importance of process safety and are incorporating it into our business-specific integrated management systems. Enterprise-wide requirements follow the industry-recommended practice (American Petroleum Institute Recommended Practice 1173) for pipeline safety management systems.
Process safety incidents involve an unexpected or uncontrolled release from a pipeline system or processing facility, sometimes involving an injury, fire or explosion resulting from release or leak of hazardous material. They have the potential to claim lives, impact the environment, and have far-reaching and long-lasting consequences. Enbridge investigates our process safety incidents to learn what controls and safety barriers failed―and why―in order to make changes to our assets and safety management system that will prevent similar failures in the future.
Managing Hazards
How the integrity of a pipeline is managed depends on the threats the pipeline faces. Not every pipeline is subject to the same threats and stresses, so Enbridge employs a wide range of risk assessment, inspection and surveillance techniques to identify threats and hazards and then selects the right combination of controls and safety barriers to preserve integrity over the life cycle of the pipeline. The process involves continual learning. As inspection technology, pipeline materials and construction practices improve with time and new data on threats and pipeline condition are gathered, our methods of maintaining fitness for service evolve. For more information please visit: http://www.enbridge.com/about-us/safety/operations
THREATS | KEY PRIORITIES | HOW WE TAKE ACTION |
---|---|---|
|
|
Design and Construction
Monitoring and Prevention
Leak Detection
|
For more details on our ongoing actions to maintain the fitness of our systems and detecting leaks, please visit the following pages on enbridge.com: Crude Oil and Liquids Pipeline Systems Integrity; Crude Oil Pipeline Monitoring; Operations; and Natural Gas Systems Integrity.
Safety is the very foundation of our business at Enbridge, and we use a multi-pronged approach to pipeline safety that includes robust inspections, maintenance and 24/7/365 monitoring.
On top of those multiple prevention activities, we also take an industry-leading approach to leak detection—in a variety of ways:
- We monitor our pipelines for possible leaks using multiple computerized systems, each with a different focus and each using different technology, resources and timing. Together, these methods provide overlapping and layered leak-detection capabilities.
- We conduct visual right-of-way surveillance—both ground and air patrols—to watch for potential issues.
- And we actively research, test and assess the best new leak detection technologies—from forward-looking infrared (FLIR) cameras, to fiber optic cables and acoustic tools.
In 2017, the Data, Detection and Diligence series on our @enbridge blog channel looked in depth at several of our leak detection initiatives, including:
- regularly scheduled fluid withdrawal tests;
- side-streaming, or “blind tests,” that put our alarm systems, people and processes on the spot;
- our multiple overlapping Computational Pipeline Monitoring (CPM) systems, chosen for sensitivity, reliability and speed; and
- our pipeline simulator training program, which helps our control center operators sharpen their skills.
To learn more, please see our Leak Prevention and Detection Fact Sheet.
Industry Leadership
We believe that industry leadership is essential to our safety and reliability strategy because it promotes vigilance and critical self-evaluation, and it drives us to continually improve the safety of our operations and work practices. Part of our leadership means taking an active role in promoting best practices in system integrity, leak detection and damage prevention through industry associations, development of national standards and recommended practices, research and development in technology, and management practices that can improve our layers of protection.
Enbridge was recognized for its advancement in quality within the energy pipelines industry. https://www.youtube.com/watch?v=Ua67azIrKCg
2017 Performance
Preventing Spills, Leaks and Releases
Our objective is to prevent all liquids spills and leaks and natural gas releases and leaks. Following an incident, an investigation occurs to identify the layers of protection that failed, the causes and contributing factors so that corrective actions can be taken to strengthen our safety systems. Following are details on the recent overall performance of Enbridge’s three core businesses.
The integration of Spectra Energy has approximately doubled the asset base of Enbridge; which has had a corresponding effect on the number of incidents that occurred across the new Enbridge system, essentially doubling the number of process safety incidents in 2016 from 24 to 47 in 2017 (Tier 1 and Tier 2 incidents).
Definitions used in this section
For the purpose of our 2017 Sustainability Report, we include incidents that are significant and reportable to our Board of Directors. :
- Significant – Significant incidents (termed Tier 1 events) are commodity releases with greater consequences than Tier 2 events.
- Reportable – Other Reportable incidents (termed Tier 2 events) are commodity releases with lesser consequences.
- Enbridge’s full definitions can be found in our Note to Readers.
The harm done in a release (such as an injury or a fire) often dictates classification of an event at a higher tier than the volume released would. Similarly, our management may decide to upgrade how we classify any event—including those that did not result in any spills, releases or harm, but that were potentially serious—to a higher tier if they deem doing so to be prudent. As such, the incidents that we include in this report have not all resulted in a spill or release.
Liquids Systems
In 2017, we delivered more than 3.7 billion barrels of crude oil and natural gas liquids. We experienced 13 reportable spills on our liquids systems in Canada and the U.S., which compares with 8 in 2016 and 14 in 2015. The total volume from the spills in 2017 was 8,470 barrels, compared with 657 barrels in 2016 and 480 barrels in 2015. Based on the volumes spilled and our gross delivery volumes, we achieved a safe delivery rate of 99.9998 percent in 2017.
The increase in volume spilled is largely attributable to a significant incident that occurred in February 2017. A contractor working for a third party struck Enbridge’s Line 2A during a directional drilling operation. The incident resulted in the release of more than 6,000 barrels of condensate blend. The product was confined to the sub-surface and two large excavations that were present in support of the directional drilling operation. Response operations commenced immediately. No air quality risks were identified. Approximately 6,100 barrels of product was recovered, and contaminated soil was remediated through excavation and in-situ treatment.
Information on other significant incidents is included at the end of this section.
Number and Volume (Barrels) of Reportable Spills (Tier 1 and Tier 2), and Volume of Reportable Off-Property Spills (Barrels), on Enbridge’s Liquids Systems
Number of reportable liquids spills | Volume of reportable liquids spills (barrels)2 | Volume of reportable off-property spills (barrels)2,3 | |
---|---|---|---|
20151 | 14 | 480 | 17 |
2016 | 8 | 657 | 23 |
20174 | 13 | 8,470 | 7,086 |
1We have restated the values from the original report for our 2015 “Number of reportable liquids spills” and “Volume of reportable liquids spills (barrels)” so that they align with our definition for Reportable Incidents (i.e., Tier 1 and Tier 2 process safety events that we are required to report to Enbridge’s Board of Directors). For more information, please see the Note to Readers.
2“Number of reportable liquids spills”, “Volume of reportable liquids spills (barrels)” and “Volume of reportable off-property spills (barrels)” are subsets of both the “Reportable (Tier 1 and Tier 2) Process Safety Event – Liquids Service” category and of the “Significant (Tier 1) Process Safety Events – Liquids Service” category.
3Includes volumes released off-site of Enbridge’s property.
42017 reflects Spectra Energy and Enbridge assets as a combined company.
Natural Gas Systems
In 2017, we transported and distributed more than 8,200 billion cubic feet of natural gas through our natural gas pipelines and our natural gas distribution network. In 2017, we experienced 34 reportable (Tier 1 and 2) process safety events, of which 18 involved a release of gas from process equipment on our natural gas systems. Of this total, we experienced six significant (Tier 1) process safety events.
Reportable and Significant Process Safety Events Involving Natural Gas
20151 | 2016 | 20172 | |
---|---|---|---|
Reportable (Tier 1 and Tier 2) process safety events | 18 | 9 | 34 |
Significant (Tier 1) process safety events | 3 | 2 | 6 |
1 We have restated the values for our 2015 “Reportable (Tier 1 and Tier 2) process safety events” and “Significant (Tier 1) process safety events – gas service” such that they align with our definition for Reportable Incidents (i.e., Tier 1 and Tier 2 process safety events that we are required to report to Enbridge’s Board of Directors). For more information, please see the Note to Readers.
2 2017 reflects Spectra Energy and Enbridge assets as a combined company.
Natural Gas Utilities
In 2017, our natural gas utilities business segment, which provides reliable natural gas service to about 3.7 million customers in Ontario, Quebec and New Brunswick, delivered more than 1,644 billion cubic feet of natural gas.
As included in the table above, we experienced 4 reportable process safety incidents in 2017. A large number of small leaks are detected on our utilities network each year because of the significant number of natural gas delivery points, and because much of the network is located in ever-changing, ever-growing urban areas. However, in the vast majority of cases these below-ground or outside leaks are not hazardous due to the low delivery pressure on the system, small line capacity and odourization, which serves as a warning sign.
The low-hazard nature of these small leaks means that the majority fall below our reportable (Tier 2) process safety event criteria. Leaks due to third parties damaging pipeline assets make up a significant portion of these releases, so to help stem those, Enbridge has an extensive public education program for pipeline awareness and safe digging. Enbridge also supports and is a member of one-call/locate services.
Summary of 2017 Natural Gas Releases in Enbridge’s Gas Utilities,
Damages per 1,000 Third-party Locate Requests on Enbridge’s Natural Gas Distribution Network – 2015-2017
20151 | 2.41 |
20161 | 2.17 |
2017 | Enbridge Gas Distribution: 1.79 Union Gas: 2.16 Gas Utilities combined: 1.92 |
1Damages/1000 locates for Enbridge Gas Distribution only.
The following Tier 1 releases reflect the 10 significant incidents on all of our liquids and natural gas systems.
Date and Location | Description of Significant Incidents Involving a Spill or Release |
---|---|
January 14 – Missouri | A flange between the mainline and station inlet valve leaked, resulting in a release of approximately 450 barrels (bbls) of crude oil. Our Edmonton Control Center detected the release and an onsite Enbridge employee immediately confirmed it. The pipeline was shut down and isolated. Some oil migrated off site but was contained. The cause was determined to be a girth weld failure. |
February 17 – Edmonton area | A contractor working for a third party struck Enbridge’s Line 2A during a directional drilling operation. The incident resulted in the release of more than 6,000 barrels of condensate blend. The product was confined to the sub-surface and two large excavations that were present in support of the directional drilling operation. Response operations commenced immediately. No air quality risks were identified. Approximately 6,100 barrels of product was recovered, and contaminated soil was remediated through excavation and in-situ treatment. |
June 8 – subsea pipeline, Gulf of Mexico | Natural gas was detected leaking from a subsea pipeline. The pipeline was shut in until repairs were made. The cause of the leak was determined to be internal corrosion. |
April 18 – Alberta | Enbridge personnel discovered oil within the concrete containment of the Manifold 211 booster units at the Edmonton Terminal. Approximately 553 bbls of oil had been released into secondary containment. The cause of the release was determined to be internal corrosion of idled piping. |
July 1 – Texas | A gas plant experienced a fire on the glycol regeneration skid. An emergency shutdown of the facility was executed. Plant operators extinguished the fire with aid of a local fire department. There was localized damage to wiring, controls and insulation (of sufficient value to classify the incident as a Tier 1 event), but there were no injuries or off-property consequences. |
July 15 – Oklahoma | Enbridge employees discovered oil on the surface of a drainage catchment within the Cushing Terminal. It was determined that the release point occurred on a below-grade transfer line. Immediate remediation consisted of isolating the transfer line segment and installing a leak clamp. All crude oil was contained on site. |
July 25 – northeast British Columbia | While collecting a sample for an inspection, a worker checking a valve position was splattered by molten sulphur on the hand and lower torso. |
August 18 – Texas | A contract mechanic was performing a compression test on a compressor at a gas plant when hydrocarbon vapors ignited and a flash fire occurred under the mechanic’s feet. The contractor was treated for minor burns to his face. The investigation identified that the braided exhaust hose had a break in the steel cord, and the spark plug leads in the vicinity of the hose provided the ignition. |
October 11 – British Columbia | Gas Control received a report from the Chilliwack Fire Department regarding a loud noise in the South Sumas area. An Enbridge employee was dispatched and identified a body bleed on a valve venting to an atmospheric vent stack. The employee closed the body bleed and notified gas control that the release was stopped. |
December 17 – Pennsylvania | After receiving a report of the smell of gas, Enbridge located a leak on a buried flange on Line 1-B. The line was isolated and blown down to repair the leak. The cause of the leak was determined to be a damaged gasket. |
Maintaining the Integrity of All of Our Pipelines and Facilities
Because our core business is to safely transport hazardous materials through a network of pipelines, we continually improve the methods we use to prevent and detect leaks and releases.
We are committed to investing in our system fitness programs and our leak-detection and survey programs to achieve our goal of zero spills, leaks and releases. Advancements in predictive (reliability) modeling, data analysis and improved efficiency in carrying out these activities are enabling us to continually enhance the safety and fitness of our systems while optimizing our expenditures.
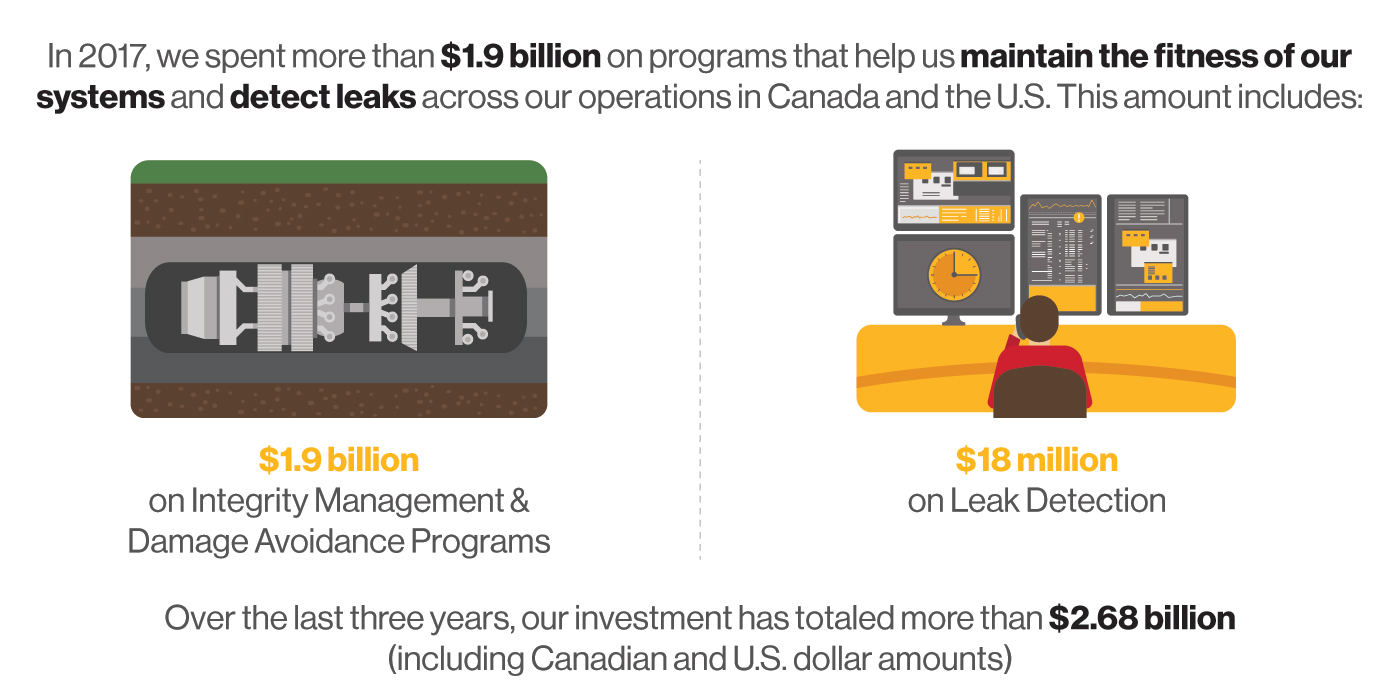
In 2017, we spent more than $1.9 billion on programs that help us maintain the fitness of our systems and detect leaks across our operations in Canada and the U.S. This amount includes $1.937 billion spent on maintaining system fitness through integrity management and damage avoidance programs* and $18 million spent on leak detection (Canadian dollar amounts). Over the last three years, our investment has totaled more than $2.68 billion (including Canadian and U.S. dollar amounts).
* In our Sustainability reports prior to this 2017 report, we did not include damage-avoidance spending in our total system-fitness expenditures.
* In our Sustainability reports prior to this 2017 report, we did not include damage-avoidance spending in our total system-fitness expenditures.
Monitoring for Leaks in our Liquids Systems: LP continues to improve its leak detection capability with enhancements to its computational pipeline monitoring (CPM) system, which collects data from strategically located flow meters, and pressure and temperature sensors along its pipelines. In 2017, we improved CPM reliability performance for the seventh consecutive year, representing an 80 percent cumulative enhancement over that time period.
LP also advanced deployment of several enhanced leak detection methodologies to improve its leak detection capability during pipeline running and shut-in conditions. Developed internally, these advanced leak detection alarming algorithms are resulting in improved capability to detect small leaks along our liquids system. Deployment of the new shut-in method has been completed to all mainline liquids pipelines. Deployment of the leak detection method for monitoring small leaks during running conditions is partially completed with a full in-service date later in 2018. These mainline pipelines are monitored and managed from our control center in Edmonton.
Leak Survey Management of our Gas Distribution Network: Each year, we conduct leak surveys of our natural gas distribution systems. This process involves reviewing the current year’s programs and targeting high-risk areas for follow-up on a more frequent basis. In 2017, we conducted leak surveys on more than 25,000 kilometers (15,500 miles) of distribution mains in our Ontario franchise area and in the Gazifère system in Quebec. We also surveyed more than 690,000 services (the lines used to carry gas from the mains to customers’ residences), which represent about 19 percent of our total gas services. In 2017, we spent $3.1 million on leak inspection and survey programs in Canada and the U.S.
In-line Inspections (ILI) and Integrity Digs: Each year, we conduct a significant number of pipeline inspections using sophisticated tools that incorporate leading imaging and sensor technology. These are capable of scanning for features that could indicate potential problems related to corrosion, cracking, mechanical damage, deformation, or manufacturing or construction defects. Our inspections allow us to monitor the physical condition of our pipelines from the inside and outside, and to gather the information we need to keep our systems fit. If the ILI finds an anomaly in the data (a sign that there could be a defect or flaw in the pipeline), that portion of the pipeline is dug up, inspected and repaired. Given the importance of making sure our ILI tools and defect models are accurate, all data from digs, whether or not a defect was found, is used to improve our understanding of how defects behave and pipelines age over time.
In-line inspections are only one example of pipeline inspections. Other integrity verification techniques used by Enbridge include: pressure tests, corrosion surveys, depth-of-cover surveys, crossing inspections, external corrosion direct assessment, and visual and ultrasonic inspection of above-ground facilities. In total, we performed over 26,700 integrity inspections of its pipeline system in 2017. In addition, we made more than 84,000 checks on the cathodic protection systems that passively protect our pipelines from corrosion.
Summary of Pipeline Inspections across Enbridge, 2017
Number of pipeline inspections1 | Total kilometers(miles) of pipeline inspected | Number of in-line inspections using smart pigs | Number of integrity digs |
---|---|---|---|
26,719 | 34,141(21,214) | 349 | 1,769 |
1 The number of pipeline inspections includes integrity digs, in-line inspections, hydrostatic pressure tests, corrosion direct assessments, inspections completed on bridges, inspections completed on slopes and water courses, and other inspections completed, such as storage-well integrity inspections and valve inspections. Our CSR & Sustainability reports prior to this 2017 report have included primarily in-line inspections.
Maintaining the Fitness of Our Systems and Detecting Leaks Performance Data Summary
20151 | 2016 | 20174 | |
---|---|---|---|
Number and Volume (Barrels) of Reportable Spills (Tier 1 and Tier 2), and Volume of Reportable Off-Property Spills (Barrels), on Enbridge’s Liquids Systems | |||
Number of reportable liquids spills | 14 | 8 | 13 |
Volume of reportable liquids spills (barrels)2 | 480 | 657 | 8,470 |
Volume of reportable off-property spills (barrels) 2, 3 | 17 | 23 | 7,086 |
Reportable and Significant Process Safety Events Involving Natural Gas | |||
Reportable (Tier 1 and Tier 2) process safety events | 18 | 9 | 34 |
Significant (Tier 1) process safety events | 3 | 2 | 6 |
Damages per 1,000 Third-party Locate Requests on Enbridge’s Natural Gas Distribution Network | 2.415 | 2.175 | Enbridge Gas Distribution: 1.79 Union Gas: 2.16 Gas Utilities Combined: 1.92 |
Summary of Pipeline Inspections across Enbridge | |||
Number of pipeline inspections6 | 194 | 15,681 | 26,719 |
Total kilometers(miles) of pipeline inspected | N/A | 29,195(18,141) | 34,141(21,214) |
Number of in-line inspections using smart pigs | N/A | 193 | 349 |
Number of integrity digs | 1,575 | 1,306 | 1,769 |
1We have restated the values from the original report for our 2015 “Number of reportable liquids spills” and “Volume of reportable liquids spills (barrels)” so that they align with our definition for Reportable Incidents (i.e., Tier 1 and Tier 2 process safety events that we are required to report to Enbridge’s Board of Directors). For more information, please see the Note to Readers.
2“Number of reportable liquids spills”, “Volume of reportable liquids spills (barrels)” and “Volume of reportable off-property spills (barrels)” are subsets of both the “Reportable (Tier 1 and Tier 2) Process Safety Event – Liquids Service” category and of the “Significant (Tier 1) Process Safety Events – Liquids Service” category.
3Includes volumes released off-site of Enbridge’s property.
42017 data accounts for Enbridge and Spectra Energy as a combined company.
5Damages/ 1000 locates for Enbridge Gas Distribution only.
6The number of pipeline inspections includes integrity digs, in-line inspections, hydrostatic pressure tests, corrosion direct assessments, inspections completed on bridges, inspections completed on slopes and water courses, and other inspections completed, such as storage-well integrity inspections and valve inspections. Our CSR & Sustainability reports prior to this 2017 report have included primarily in-line inspections.